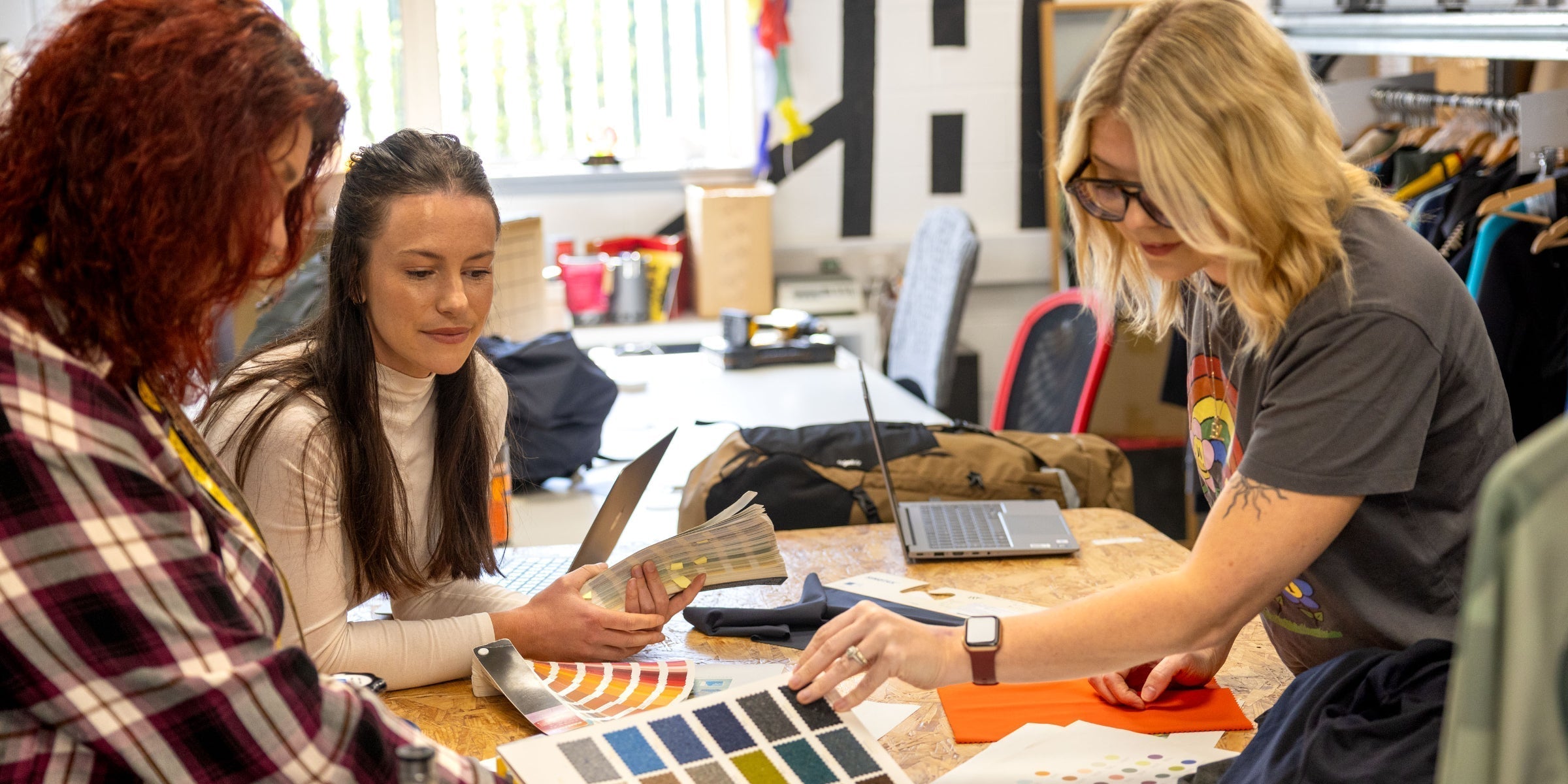
Great outdoor clothing has technicality built in from the ground up. In this article we will look at the team and the skills needed to make this happen.
Most people don’t think about who designed their waterproof jacket, or the hands that shaped their favourite pair of leggings. But every seam, zip, and choice of component started with a pencil sketch, a prototype, and someone asking:
“How do we make this better?”
Who else looks customers in the eyes, listens to their problems and develops gear for the world's toughest environments? Store visits and customer feedback along with constant testing help us tweak and develop our clothing to work how and when you need it.
We're proud to have a small but hugely talented design team all based here in the UK. At Alpkit, that someone is Lauren, Emily and Becky – the team quietly shaping the clothes that shape our outdoor adventures. And we want you to meet them.
Lauren - Head of Clothing Development
Lauren leads Alpkit’s clothing design team. She’s the one balancing ideas, feedback, function, and that elusive Alpkit feel. The stuff that’s rugged but minimal. Technical but not overdone. Clothes that work with you.

With over 17 years' experience in clothing design and development with a 1st BA Hons degree in fashion and textiles buying from the University of Huddersfield, Lauren has worked with several outdoor companies which has enabled her to travel the world meeting factories and suppliers who produce outdoor clothing.
"My personal strength is garment construction and fit, it's the most important part of the development process- getting that perfect fit and making sure the product stands the test of time."
Lauren learnt to understand pattern cutting and fashion design from a very young age, "my Mum is an amazing seamstress and also studied fashion design and worked in the industry, she taught me garment construction, but much to her annoyance I cannot sew as well as she can, I don't have her patience."
Emily - Clothing Developer
Emily has worked in the industry for over 9 years since graduating with a 1st BA Hons degree in Fashion & Textile Design. Her first jobs were in design, retail and sewing factories both on the sewing line and as a sample technician. It’s safe to say she has had an eclectic overview of the industry.

"I love designing clothing which makes people feel great when they put it on. Colour is at the heart of my design process, and I focus on the tiny details which make a real difference in how a garment looks and feels. I come from a creative family of writers and artists and have always known I wanted to work in clothing design & development."
So how did she end up working in the Outdoor side of the industry? "I spend most of my free time in cold water, on cold water (paddle boarding), up a mountain, lying by a river or dancing. I love to explore all sorts of ways to get my body moving and will have a go at anything! Having grown up in the beautiful Lake District, the outdoors is a part of me. I was dunked in Derwent Water at 4 months old and never looked back! Although now I look a little more peaceful when doing so…"
Becky - Garment Tech
Becky, is our garment technologist. She brings the whole puzzle together in the fit room – where theory meets reality. Becky knows how to tweak a seam to stop it rubbing at mile 30.

Becky has 30 years’ experience in various clothing design and technology roles. Starting as a Lingerie designer, pattern cutter and grader in Nottingham. She then moved to the role of Garment & Product Technologist for Ann Summers before switching to be a Corsetry & Swimwear Garment Technologist at JD Williams. Becky says "They specialise in larger cup sizes, so the fitting and support required on those products can be very challenging."
It is little wonder we talk about our clothing being designed or engineered. Our clothing has to move with the body, it has to be supportive, close fitting, durable, it has to insulate, shed water, be repairable. Technicality considered at every stage.
Why they do it
“The best part of my job is researching new fabric innovation.” says Lauren. “I enjoy developing technical fabrics to enhance the wearer experience whilst doing the thing they love the most- running, climbing, cycling etc.”

Lauren has only been with us for a few months but she has already been in the front line fielding questions from a bunch of Alpkit customers at a Meet the Designers event we hosted in our Hathersage store in March. It was well attended by outdoor enthusiasts, MRT volunteers and students all keen to gain insight into our design process - little did they know they were part of it!
Having this direct contact between our design team and customers is something that sets Alpkit apart from other brands.
"I love seeing new products develop but it’s so satisfying to resolve issues with products and know that you have made a difference on how someone is going to feel wearing and using our products." Says Becky who has had her own experience interacting directly with the end user.
What could be more personal than running a business making wedding dresses. "it was great to go through the journey with each bride and help make their dreams come true. I managed to let my creative juices work there, helping design the bespoke dresses and making the Swarovski tiara’s."
From sketchbook to summit
So how does a piece of Alpkit clothing actually get made?
It starts with need. From there it’s ideas, sketches, choosing fabrics, building test samples, and then getting it outside – in the wet, in the wind, on the move.
Our clothing is specified to not only be comparable with the best, but to be the best. Gear that works as you need it to, designed to last and be repairable. We design for performance first, believing the most sustainable piece of gear is the one that works time after time, the one you trust for a lifetime of adventures.
Designed for durability. Built to be better.

Designing for movement, not just looks
"My favourite part of the job?" asks Emily, "Working with such a great bunch of people and playing a part in shaping the future of outdoor gear."
What sets our team apart is simple: they’re designing for real adventures. The best kit disappears when you’re wearing it. It shouldn’t get in your way. It should let you go further, stay out longer, and feel better while doing it.
From the perfectly placed seams on Nessie and Baltic to the featherweight warmth of the Heiko down jacket – it’s performance that leads the way.
Sometimes it is what you don't notice that is important.

Want to get into outdoor apparel design?
If you’re reading this thinking “I’d love to do that,” the team have some advice.
“The best advice I can give to someone wanting to do what we do is to find your focus- and get really good at it.” says Lauren. “Its a competitive world out there, you need your focus and your passion to make you stand out.”
Retail experience, hand-making your own gear, learning to sew, doing side projects – all of that counts.
We are also grateful to have a strong relationship with the BSc Product Design course at Nottingham Trent University. Each year we set projects, host workshops and invite students to see our working processes. Choosing a university with close ties to business is a great way to understand commercial pressures of a working studio.
Behind every jacket, there’s a story
Next time you throw on your waterproof in sideways rain, or pull off a cold-weather camp thanks to your insulated layers – remember there’s a team behind you. Not chasing trends. Just chasing better.
Better fit. Better comfort. Better freedom to move. It is what Lauren, Emily, and Becky are stitching into every seam.